Ball mill is a critical component in cement manufacturing, contributing to effect grinding, controlled particle size and overall production quality.
Ball mills are integral to cement manufacturing, pivotal for grinding raw materials such as limestone, clay, and iron ore into fine particles essential for creating the cement mixture. Additionally, they finely grind clinker, a nodular material formed during the cement kiln stage. The controlled grinding process ensures the attainment of desired fineness, optimizing cement performance. Beyond grinding, efficient ball mill operation enhances energy savings and boosts production rates, fostering consistent quality while reducing specific power consumption and operating costs per unit of production.
ANSWRS Provide Total
Lubrication solutions to improve performance and extend the mill's lifespan, ensuring reliable operation and overall efficiency in cement production.
Salient Features Of ANSWRS Oil Circulation Systems
➢ Reduction of start-up wear
➢ Maximize the potential for hydrodynamic lubrication
➢ Installed circulation systems remove contaminants (filter) and cools the oil allowing maximized oil and bearing life.
➢ Lower operating and maintenance costs
➢ Greater dependability and reduced wear
➢ Reduced risk of lubrication related breakdowns
➢ Extended service intervals
ANSWRS expertise in complete design, engineering and manufacturing solutions for Ball Mill Application-
1. Jacking (Lift) Systems - High Pressure & Low Flow is required to be supplied to the bottom of the Trunnion before the Ball Mill is set in motion. This High Pressure lubricant lifts the mill to enable it to roll and avoid damaging metal to metal surfaces. Once lifted and rolling the lubrication (Low pressure & high flow) can be started.
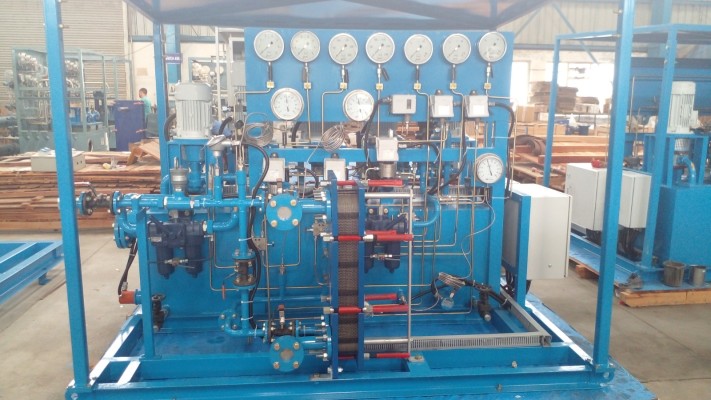
2. Lubrication Systems - Low Pressure/High Flow oil is circulated from a reservoir to the top of the Trunnion bearing. The low pressure oil coats the journal and other bearings surfaces, helping with oil wedge formation when rotation has been achieved. The high flow circuit will deliver the filtered and cooled oil to the bearing.
3. Lift & Lube Systems - Individual Jacking and Lubricating circuits can be combined in one “Lift & Lube” system. Common reservoir with individual pumps, filters, and heat exchangers as required.
4. Filtration - It is critical to remove contaminants such as dust, wear particles, water and other extraneous materials that build up during bearing operation. The Lubricant needs to be filtered to the correct cleanliness level prior to being circulated and will extend the life of the oil and Bearing.
5. Cooling - Cooling the oil will maintain the correct viscosity of oil required at the bearings,
ensuring the lubricate maintains its optimum performance level and extending the life of the oil and bearing.
6. Complete design solutions - We pride ourselves on our ability to deliver the complete engineered design solution. With over 33 years of technical experience, our dedicated team can cater for any set-up requirements and will guide you every step of the way from design to delivery. Systems that are fully enclosed can be supplied protecting the systems from the elements.
Wants to ask questions ? Please ask, ANSWRS will give answers.
Thanks & Regards | Shweta Jindal | Marketing Manager